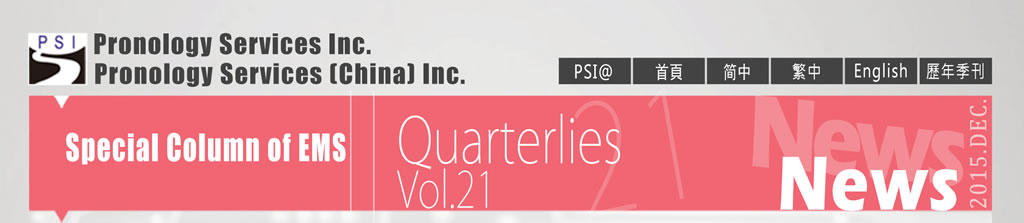
2016 improvement on procurement system
Author:Edwin Lin
It has been 2 years since switching from old ERP into TIPTOP ERP by PSI. With a view to improve the system operation, PSI continues working on better solution for the system with IT team. In the coming 2016, the major improvement of procurement system will be the management of requested parts, exceeding parts and long lead time parts. Below is the brief introduction of the procuring performance after the improvements.
- Management of requested parts (MRP : CMRT100, unique parts, new parts, monthly average Qty and safety stock, etc.)Improving the procurement request program with MRP CMRT100. The system will generate the Qty of requested parts automatically under consideration of the current status of unique parts, new parts, monthly average Qty, safety stock and so on. It greatly reduce the error made by manual maintenance, improving the accuracy of parts applying, reducing the procurement of excessive parts for better safety stocking. Through this we achieve perfect auto-management.
- Management of excessively procured parts (simulation of shortage of parts -> improved management on material control and procurement)First we turns to auto-management of exceeding parts from the current manual-management by material control department. The material shortage simulation list generated by MRP calculation will generate the exceeding parts list. With the weekly feedback of the reason to purchase the exceeding parts, the system precisely monitoring the on-going exceeding parts. It reduces the error of manual work, reduces the stocking cost for PSI and the customers. That is the achievement of auto-management.
- Report of long lead time parts
Based on the average demand of last 6 months through a weighted calculating method, the system will generate a “suggested stock quantity” that will perfectly satisfy customer’s demand for urgent orders. It will prevent the shortage of parts or buying the in-stock parts for higher price from the suppliers. This leads a great saving of customer’s expenditure for parts, and make our parts supply more competitive in the market.
The report provides 3 management methods for the long lead time parts. It offers multiple management methods to fit different customers’ demand.
- (1) Standard report:
- Based on the average demand of last 6 months through a weighted calculating method, the system will generate a “suggested stock quantity” that will perfectly satisfy customer’s specific preference and unique demand.
- (2) Cut off the higher-than-average demand :
- The goal of this standard report is to cut off the higher-than-average demand of special projects which may mistakenly increase the actual average monthly demand!
- (3) Cut off the suspended production orders:
- The standard report will cut off the suspended production orders to avoid procuring the excessive parts for the rare projects.
PSI is heading for better service quality by the improvement on procurement system. It enables PSI becomes more competitive and achieves better growth under the unstable worldwide economic environment, with great hope to create win-win situation for both PSI and customers.

