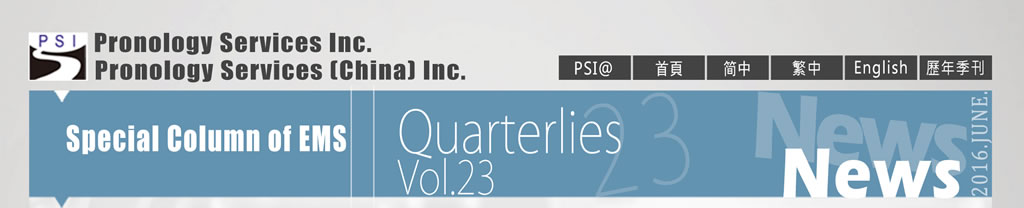


Work Order Closure & Enhancement of Completion Rate
Author: Maggie Chen
In the manufacturing industry, there are some production models of production orders, such as planned production or subcontractor production.
Usually, the current order patterns generally face challenges of low volume, high mix and short lead time.
Management of materials, capacity and cost of control is even more important for the company.
How do we manage the materials, capacity and cost of control? We can enhance the work order closure and completion rate to achieve the goals. With the goals established, we build the system programs and report management for preproduction/in production/postproduction stage to enhance the accuracy and timeliness on the production management. And then we can follow customer’s demand to manage the process and arrange the production schedule by work order to increase the capacity utilization and shorten the manufacturing cycle.
1. | Before having the work order in production, we confirm the validity of each order first. For example, the start work data, delivery date, materials status and special requests. It helps us conduct a good evaluation and understand the needs of each customer’s delivery and order status. |
2. | In production of work order, we can also make a reference from the evaluation status before production to arrange start time accurately and efficiently. We can have thorough management for each work order output time, avoid discharge production line due to material shortage, which has a impact on output time, causing the production to stop. We can have precise management for customer’s demand and quantity/cost of the inventory. |
3. | We can do the multi angle analysis for abnormal work orders by weekly collation, monthly statistics report, and quarterly reviewed meeting with related department. |
The management of goals by Production Control Team:
1. | The use of system reports for control of helps approaches with each work order effectively, from the start to closing time. An abnormal status can also be found in real time in the process of each stage. And then we are able to track the status of balance quantity and make a closure in advance. |
2. | Management of the iInventory for abnormal work order: set the related report analysis, reviewed and improvement by weekly, monthly and quarterly. - Process (S + D): Process exceeding the predetermined 5 calendar days from the start day is required to settle the semi-product. It needs to be transferred and finished. A total duration of more than six days is deemed abnormal. - Process (S + D + T1 + R): Process exceeding the predetermined 7 calendar days from the start day is required to settle semi-product. It needs to be transferred and finished. The production duration over 15 days (test and repair process included) as seen as an abnormal event. - Process (T2 + A + P): Process exceeding the predetermined 12 calendar days for the start day is required to settle product. It needs to be transferred finish and finished. The production duration over 20 days (test, assembly and pack process included) is seen as an abnormal event. |
3. | Work order tracking management : We set the work order closure and completion rate at 85% for enhancement. |
Work order management program by PSI :
1.Pre-production management : csfp402, csfr102
2.In production management : csfp602, csfp150,csfp412
3.Post-production management : csfp420, csfp430,csfp440
2.In production management : csfp602, csfp150,csfp412
3.Post-production management : csfp420, csfp430,csfp440
Program Code | Program Name | Function | Note |
csfr020 | Work order auto build list | System builds the work order automatically at fixed time daily and generate a list to PC staff for checking abnormal and normal work orders | |
cxmp451 | New work order maintenance by PC | For customer order request, PC people can build the work order in real time by entering data into the system manually | |
csfi301 | Work order maintenance | For customer order change, PC people can revise the work order quantity and close work order by entering data into the system manually | |
csfr009 | Work order revised check report | System can generate a report to PC people for checking the revised work order information at fixed time daily | |
csfp402 | Sales order schedule (By Sales) Sales order schedule (By PC) | System executes sales order distribution by automatically combining work orders and separating two reports of Sales and PC. By Sale: Sort by delivery date of sales order By PC: Sort by kitting date of sales order. Use of colors in report reminds PC people for an effective management. It helps confirmation of the production started time , abnormal work order distribution, and delivery L / T control. It also generates feedback of the tracking status into system. The schedule report can be confirmed. The production time for each work order can inform sales people in advance to process when there is an abnormal status | 1. Pre-production management |
csfr012/csfr014 | not started work order after 6 months (By PC)/(By Sales) | System can send the report to PC people automatically for checking on every Friday. To inform Sales people and confirm if they are effective work order. (By Sales) Confirm each work order status and generate feedback of the status into system. (By PC) Confirm each work order status and generate feedback of the status into system. | 1. Pre-production management |
csfp602 & csfp150 | Production Schedule Simulated Operation (YT) | Production Schedule Simulated Operation (YT)
System can provide the work time for each work order and process to calculate the total production time by each work order that is convenient for PC people to arrange production schedule.
PC people follows the order’s started and delivery date to arrange the production schedule and provide the production sequence, output time, quantity to production line. PC people can track the production status according to schedule. Use of colors in report reminds PC people of confirming the production schedule and adjusting the output time when the order’s shipping information has been modified. | 2. In production management |
csfp412 | Shipping schedule(By PC) | System can provide the shipping request for each work order daily, which is convenient for the tracking of shipping status and arrangement of shipping schedule by PC people. Use of colors in report reminds PC people of track status and feedback status into system when order’s shipping information, abnormal time or transferred quantity has been modified. System can send the report to PC people automatically for checking at 8:30 and 16:30 daily. If there is an abnormal status, PC people will confirm orders and inform sales people within delivery 3 days. | 2. In production management |
csfp422 (Planning) | WIP Stock (By PC) | Currently, the program is still in plan by IT team. The purpose of the system is that it can auto-deduct quantity according to production work order transferred list and shipping list, and auto-send a stock report to people at specific time daily. People can know the stock distribution in process for each work order in real time. | 2. In production management |
csfp430/csfp440 | Balance quantity report by work order (By PC) Balance quantity report by work order (By Production) | For the quantity control by work order of production L/T exceeding 90 days, PC people will track the root cause Use of colors in report reminding people to pay attention on this. It also tracking status and write-back status into system by PC and production line. Make a notification of abnormal balance quantity management to related department on Friday weekly. Abnormal status analysis and it is reviewed during quarterly meetings. | 3. Post-production management |
csfr013 | Work order closed & completion rate report | System can send the report automatically after financial billing monthly. PC people will confirm if the goals are achieved. | 3. Post-production management |
