
Ordering arrangement automation, providing customer real-time service
Author: Winny Liang
In the era of modern automation, production and sales through computer systems ERP, EDI ... and etc. method, to help manufacture aspect, business sales and client aspect, be efficient and correct to complete production orders and punctual delivery, even more in this competitively electronics' industry become the basic skills to customer service, underneath is our share to process of customer orders and instant supply of related messages.
1. Order management:
- When receiving the customer's order, salesmen will via ERP system' cxmp001 all can able automatically transfer customers' different forms of orders through EMAIL or EDI into the company's ERP system.
- At the same time use ERP cxmp460 (Figure 1) manage orders all customers need and related information; including shipping information, BOM issues, change the work order materials ... and other information, throughout this system platform for immediate delivery to each of the factory units. At the same time, all the factory' units quickly grasp important customer information through MIS, ERP or Kanban system to execute and confirmed in the production process.
Figure 1: Cxmp460
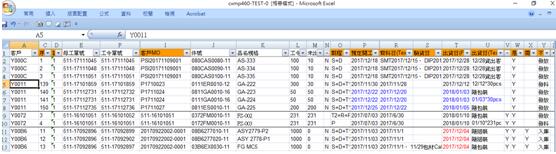
2. Instant messaging:
PSI salesmen in addition to confirming provide the status of the work orders arrangement for customer to confirm by weekly, we also at the same time provide a set of account and password to clients, through PSI website to login our system, provide clients to search with the following information online:
- Through PSI's MIS system real-time information as (Figure 2), can query order information (Figure 3) and shipping information (Figure 4).
- Through the lack of material simulation reports (Figure 5), you can instant realize the status of the work order materials preparation condition, and in time to do work orders materials preparation and shipping time adjustment and processing.
Figure 2: PSI self-developed MIS system
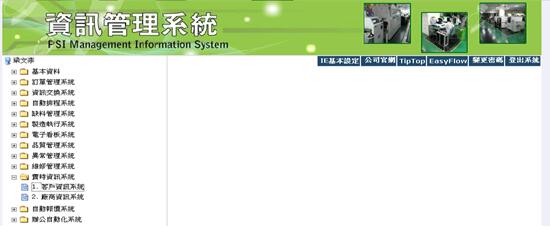
Figure 3: Order Inquiry

Figure 4: Shipping status inquiry
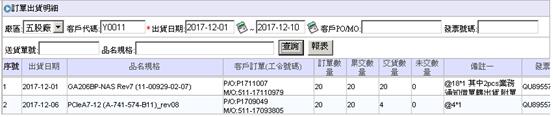
Figure 5: Simulation lack of material
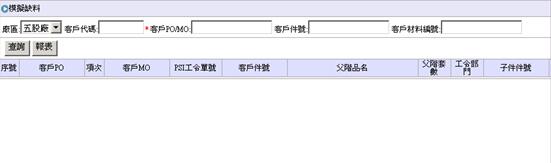
PSI self expects to provide customers with more immediate and efficient automated management systems and information, therefore to create a win-win situation between customers and PSI, and win customer trusted, PSI also hopes to establish a solid and lasting partnership with each other.
