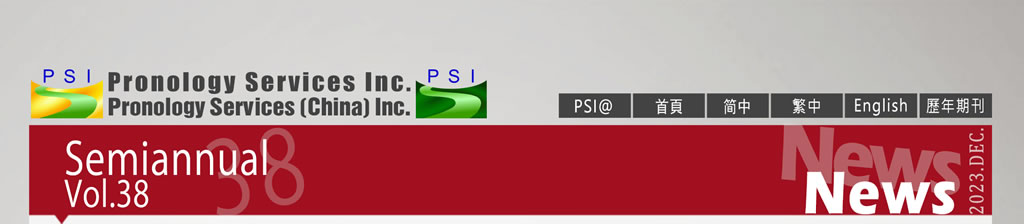
Comprehensive optimization of customer real-time information system
Author: Winny
The electronic information industry is an industry that is changing rapidly. If you don’t advance, you will retreat. We rely on the electronic information industry, and we also work side by side with our partners to not fall behind, so that our peers can complement each other and advance step by step. Information transparency and sharing promote long-term cooperation. We provide partners with an information exchange platform to achieve technical and comprehensive integration.
First of all, I would like to share PSI’s real-time system development process with my partners. Everyone is welcome to listen. Since our real-time system is like a TV series, growing and optimizing with everyone, our journals will start to display and introduce the current development and use status from 2020. The following is for everyone to review. New optimization content will be shared with you in detail.
PSI’s real-time system is log in from Pronology official website http://www.pronology.com.tw/
Below you can see the login screen. At the same time, it is also explained that whether you are a customer or a supplier, if you do not have an account and password, please apply to your business or purchasing window to log in. If you may be a future customer or supplier, you are also welcome to contact us.
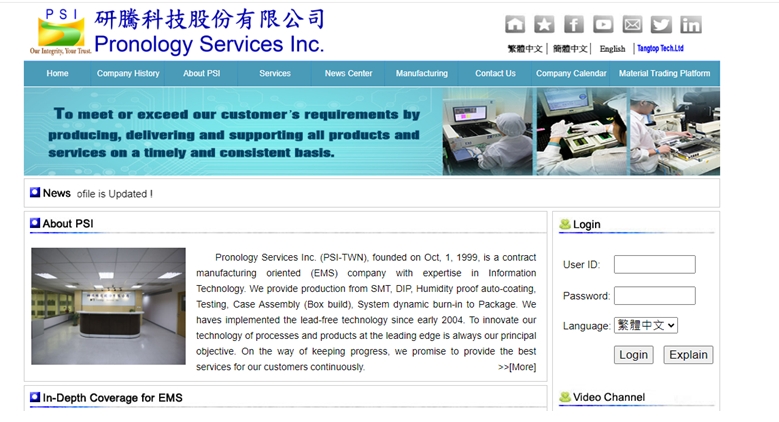
Figure 1: The screen after logging in to the system will first show you the current function screen for your reference and sharing.
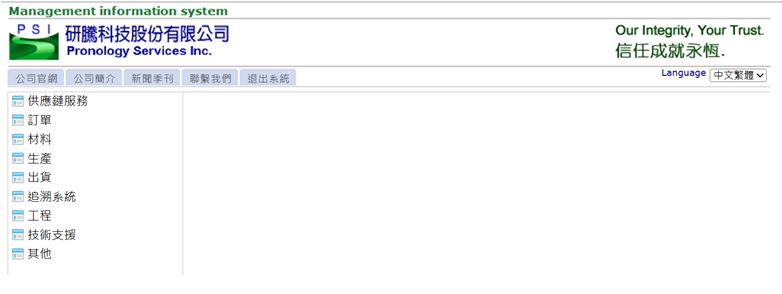
1. Supply chain services
We provide a platform for customers and manufacturers to buy and sell materials. The following is a detailed introduction to the journal for your reference
Another customer exception management platform is under construction and will be shared with everyone after completion.
Figure 2: The screen of supply chain
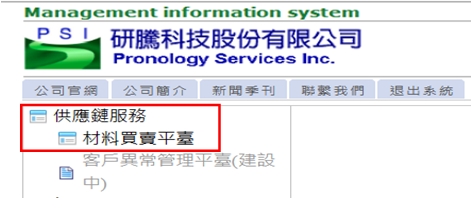
2. Order and material system
Order and material functions are compulsory courses. Please conference following journal.
Figure 3: The screen of order and material
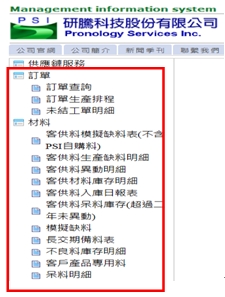
3 Production program
The system provides the production status that customers are most concerned about. The iron plate and maintenance status are explained as follows.
- Timely reporting system, customers can check the production completion reporting status of each process according to the customer's PO/MO
- For iron plates to be processed, customers can check the production completion report status of the process according to the customer's PO/MO.
- The yield and maintenance reports are under construction and will be shared with everyone after completion.
Figure 4: The screen of production program
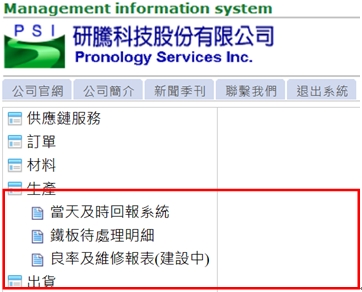
4. Shipping system
For shipping schedule and shipping details, please refer to the following journals. The following introduces to you a more convenient query with customers as the main body.
- Product shipment records: Customers can check the shipment records according to the customer's PO/MO shipment period
- Sales amount statistics table: Customers can query monthly shipment statistics records according to the year of shipment, which facilitates customers to conduct incoming sales analysis.
- Sales reconciliation details: Customers can query reconciliation details by account period, invoice number or period, which facilitates customer reconciliation and auditing.
Figure 5: The screen of shipping system
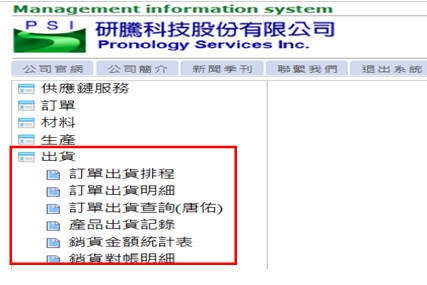
5. Traceability system
- RMA pending report: Customers can check the RMA processing status according to the RMA number
- Material traceability system: All OEM customers can check the production batch part D/C No. by period or customer part number.
- Product traceability system: System product customers can query shipping and assembly testing by pc No, SMT by lot information according to definitions
- RMA maintenance information query and report: Customers can query RMA maintenance report based on RMA number or interval.
6.Project
- Latest data list: customers can transparently share synchronized information
- BOM: Customer BOM and Pronology BOM can be queried simultaneously.
- SOP: Pronology internalized SOP sharing is under construction
- Label Format: Pronology internalized information sharing
7.Technical support
Pronology shares common materials, layout and typesetting suggestions to provide customers with design in.
8.Other
All technical documents provided by customers can be checked and compared in the cloud to facilitate exception and issuance confirmation.
As we spare no effort to continue to optimize the information platform for exchanging information with customers and manufacturers, our goal in 2024 is to interact with partners in the system, hoping to provide customers with more convenient, blind-edge and professional services in the information and Internet era. If you have any suggestions, please feel free to give them. Pronology will strive to achieve success for manufacturers and customers and continue to grow together. Thank you to all partners for their support.

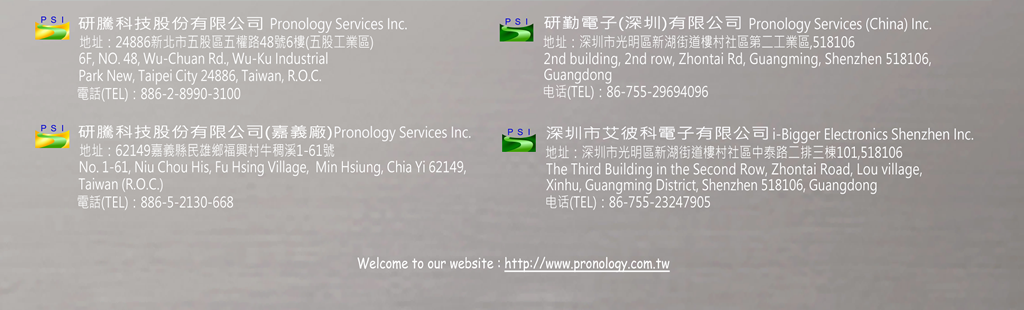